Solving the puzzle of impedance mismatching in EV part manufacturing
As the demand for electric vehicles continues to grow, induction heating engineers are increasingly being tasked with adapting production processes to accommodate EV parts. However, this presents a significant challenge, as the requirements for EV parts can be vastly different from those of traditional automotive components.
For instance, EV parts usually require a deeper hardened zone, which requires hardeners to work with lower frequency, change power, and re-design the induction coil. All of these adjustments can lead to impedance mismatching, which negatively impacts the efficiency and quality of the induction hardening process.
In this blog post, we will explore how simulation software is helping engineers overcome this obstacle and successfully adapt their hardening processes for the production of EV parts.
CENOS simulation software was invited by ASM International to present at the Heat Treat show in Monterrey, Mexico. Mario Gutiérrez Palencia delivered a presentation on the topic, which is now available as a PDF in both English and Spanish. You can find the PDF here.
The goal is to design a process that maximizes power transfer from the source (generator) to the load (inductor + workpiece). To achieve this, the load impedance should be equal to the source impedance.
There are two ways to match impedances:
- Design a coil with the needed inductance.
- Change the electric circuit of the system by adjusting capacitors to match the new inductance.
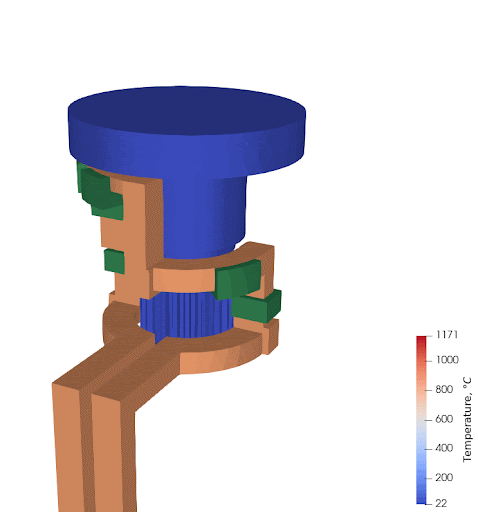
Solving the puzzle of impedance mismatching in EV part manufacturing
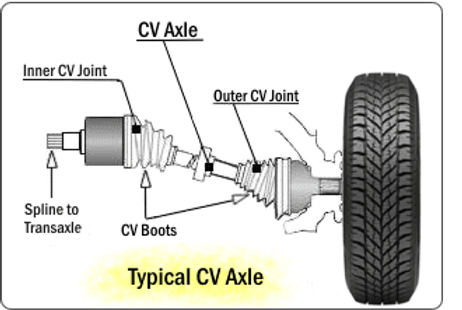
Solving the puzzle of impedance mismatching in EV part manufacturing
Let’s take a case study on a CV joint hardening. Assuming that the joints used in both internal combustion cars and electric cars have the same dimensions, the next step is to adjust the heating recipe to fit the new specifications. The new specifications require achieving a 5 mm (0.20 in) hardening zone instead of the previous 3 mm (0.12 in). The inductance should be in the 60-100 nH range as given by the generator.
The parameters for joint hardening are different for internal combustion vehicles (ICV) and electric vehicles (EV).
For ICVs, the parameters are:
- Frequency: 12 kHz
- Power: 60 kW
- Heating time: 5 seconds
For EVs, the parameters are:
- Frequency: 5 kHz
- Power: 60 kW
- Heating time: 6 seconds
Simulation software allows the calculation of hardening zone profile and inductance. Now, the user can adjust the design of the inductor and/or the hardening recipe to get the desired hardening profile and depth while keeping the inductance in the allowed range. For example, the user can add additional flux concentrators.
The software also allows the user to make an in-depth examination of the process like induced current density distribution can be traced over the heating period.
Then, the user can check back the inductance over time. As you can see from the graph, for 12 kHz heating, the inductance fits in the defined range, while for the 5 kHz version, it slips out of the range of 60 – 100 nH allowed by the power supplier. The simulation software helps the user to identify the mismatch and to re-design the inductor in a way to get it back.
Simulation is a useful tool for designing new inductors, as it can speed up the process and make it easier to predict and solve potential problems. In particular, simulation can help find the inductance of the inductor, which is especially useful for cases with irregular designs.